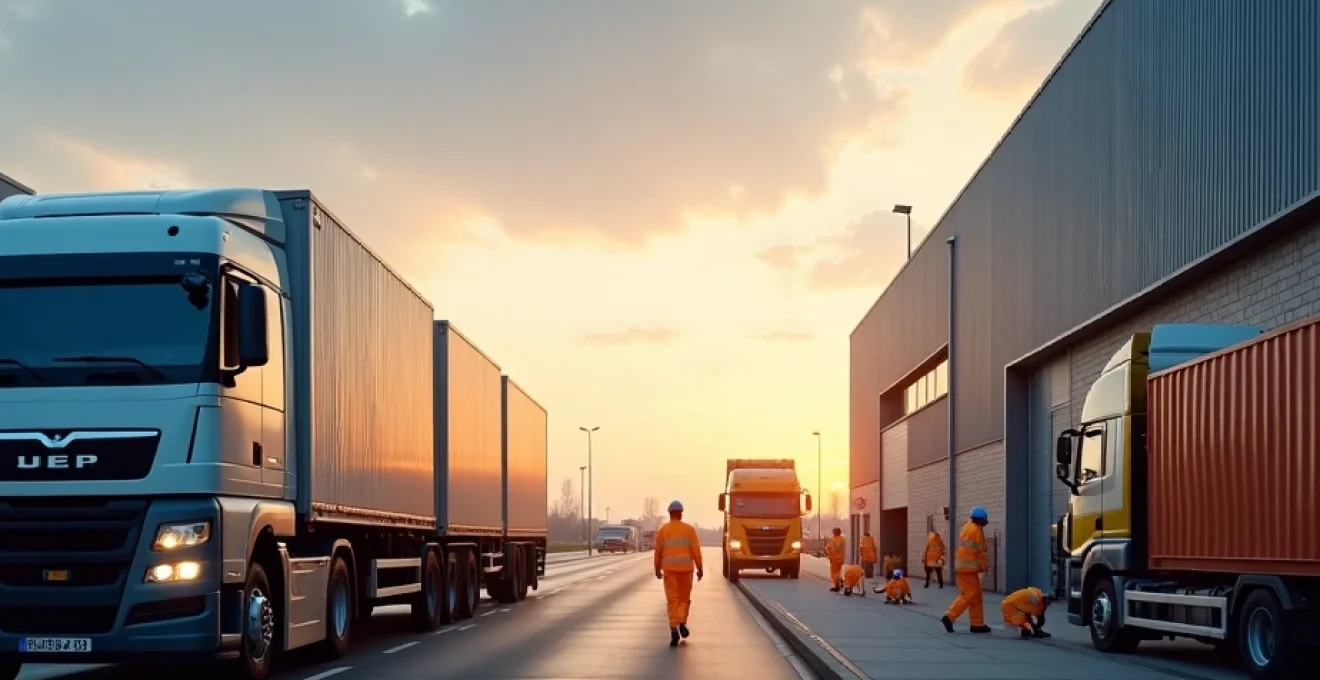
Le déménagement industriel représente un défi logistique et organisationnel majeur pour toute entreprise. Qu'il s'agisse de transférer une usine entière ou de déplacer des équipements lourds, cette opération complexe nécessite une planification minutieuse et une expertise spécialisée. La réussite d'un tel projet repose sur la maîtrise de nombreux aspects techniques, réglementaires et opérationnels. Découvrons les cinq éléments essentiels à connaître pour mener à bien un déménagement industriel.
Logistique spécialisée pour le transport d'équipements lourds
Le transport d'équipements industriels lourds et volumineux constitue l'un des défis majeurs du déménagement industriel. Cette tâche requiert une logistique hautement spécialisée et des compétences techniques pointues pour garantir la sécurité des biens et des personnes tout au long du processus.
Techniques de levage pour machines industrielles
Le levage des machines industrielles nécessite l'utilisation de techniques et d'équipements adaptés à leur poids et à leur configuration. Les grues à tour , les portiques et les ponts roulants sont couramment employés pour soulever et déplacer les charges les plus lourdes. Ces opérations exigent une expertise particulière pour éviter tout risque de dommage ou d'accident.
L'utilisation de palonniers
spécialement conçus pour répartir la charge de manière équilibrée est souvent indispensable pour manipuler des équipements aux formes complexes. Les techniciens doivent maîtriser les calculs de charges et les points d'ancrage pour garantir la stabilité durant toute la manœuvre.
Sécurisation des charges surdimensionnées sur camions plateau
Le transport des équipements industriels sur la route nécessite une attention particulière à la sécurisation des charges. Les camions plateau sont équipés de systèmes d'arrimage sophistiqués pour maintenir fermement les machines en place, même lors de trajets longs ou accidentés.
Des sangles à cliquet , des chaînes et des blocs de calage sont utilisés de manière stratégique pour immobiliser la charge. Un plan de chargement détaillé est établi pour optimiser la répartition du poids et respecter les limites légales de charge par essieu.
Itinéraires optimisés pour convois exceptionnels
Le transport de charges hors gabarit nécessite souvent la mise en place de convois exceptionnels. Ces derniers empruntent des itinéraires soigneusement étudiés pour éviter les obstacles tels que les ponts bas, les virages serrés ou les zones de travaux.
La planification de ces itinéraires fait appel à des logiciels spécialisés qui prennent en compte les dimensions des charges, les caractéristiques des routes et les réglementations locales. Cette optimisation permet de réduire les risques et d'améliorer l'efficacité du transport.
Gestion des permis de circulation spéciaux
Le transport de charges exceptionnelles requiert l'obtention de permis de circulation spéciaux auprès des autorités compétentes. Ces autorisations définissent les conditions de circulation, les horaires autorisés et les mesures de sécurité à mettre en place.
La gestion de ces permis implique une coordination étroite avec les services de police et de voirie. Des escortes peuvent être nécessaires pour sécuriser le passage du convoi et gérer la circulation. La complexité administrative de ces démarches nécessite une anticipation importante et une expertise en matière de réglementation routière.
Planification et coordination du déménagement d'usine
Un déménagement d'usine réussi repose sur une planification méticuleuse et une coordination sans faille entre tous les acteurs impliqués. Cette phase préparatoire est cruciale pour minimiser les perturbations de la production et assurer une transition en douceur vers le nouveau site.
Cartographie détaillée des flux de production
La première étape consiste à réaliser une cartographie exhaustive des flux de production actuels. Cette analyse permet d'identifier les interdépendances entre les différents postes de travail, les équipements et les zones de stockage. Les experts utilisent des outils de modélisation des processus pour visualiser ces flux et optimiser leur réorganisation sur le nouveau site.
Cette cartographie sert de base pour concevoir l'implantation optimale des équipements dans les nouveaux locaux. Elle permet également d'anticiper les éventuels goulots d'étranglement et d'améliorer l'efficacité globale de la production après le déménagement.
Séquençage du démontage des lignes de fabrication
Le démontage des lignes de fabrication doit être soigneusement planifié pour minimiser l'impact sur la production. Un séquençage précis des opérations est établi, en tenant compte des dépendances entre les différents équipements et des contraintes de production.
Ce plan de démontage identifie les équipements critiques qui doivent être déplacés en priorité et ceux qui peuvent être démontés plus tard. Il prévoit également les ressources humaines et matérielles nécessaires pour chaque étape, ainsi que les procédures de sécurité à respecter.
Stratégies de minimisation des temps d'arrêt
La réduction des temps d'arrêt de production est un enjeu majeur lors d'un déménagement industriel. Plusieurs stratégies peuvent être mises en œuvre pour atteindre cet objectif :
- Déménagement par phases pour maintenir une partie de la production opérationnelle
- Constitution de stocks tampons pour assurer la continuité des livraisons
- Planification du déménagement pendant les périodes creuses ou les arrêts programmés
- Mise en place d'équipes de travail en rotation pour accélérer le processus
Ces stratégies doivent être adaptées aux spécificités de chaque entreprise et à ses contraintes de production.
Coordination avec les fournisseurs et sous-traitants
Un déménagement industriel impacte l'ensemble de la chaîne d'approvisionnement. Une communication proactive avec les fournisseurs et les sous-traitants est essentielle pour assurer la continuité des opérations. Il est important de les informer des changements à venir et de coordonner les livraisons et les interventions en fonction du nouveau planning de production.
Cette coordination peut également inclure la révision des contrats et des conditions logistiques pour s'adapter à la nouvelle localisation. Dans certains cas, il peut être nécessaire de rechercher de nouveaux partenaires plus proches du nouveau site pour optimiser la chaîne d'approvisionnement.
Technologies de démontage et remontage d'installations complexes
Le démontage et le remontage d'installations industrielles complexes font appel à des technologies de pointe pour garantir la précision et l'efficacité des opérations. Ces outils modernes permettent de réduire les risques d'erreurs et d'accélérer le processus de transfert.
Scan 3D pour la documentation précise des équipements
L'utilisation de scanners 3D haute résolution permet de créer une documentation extrêmement précise des équipements avant leur démontage. Cette technologie capture chaque détail de l'installation, créant un jumeau numérique qui servira de référence lors du remontage.
Les données collectées par le scan 3D sont utilisées pour générer des plans détaillés, des schémas de câblage et des instructions de montage. Cette approche réduit considérablement les risques d'erreurs et facilite la planification du remontage sur le nouveau site.
Utilisation de la réalité augmentée pour le repositionnement
La réalité augmentée (RA) offre des possibilités révolutionnaires pour le repositionnement précis des équipements dans leur nouvel environnement. Les techniciens équipés de casques ou de tablettes RA peuvent visualiser l'emplacement exact de chaque machine, superposé à la réalité du nouveau site.
Cette technologie permet de vérifier les alignements, les dégagements et les connexions avant même que les équipements ne soient physiquement installés. Elle facilite également la formation des opérateurs qui peuvent se familiariser avec la nouvelle configuration de manière virtuelle.
Outils spécialisés pour le démontage non destructif
Le démontage d'installations complexes nécessite souvent des outils spécialisés pour éviter d'endommager les équipements. Des extracteurs hydrauliques
, des découpeurs plasma
et des systèmes de desserrage par induction
sont utilisés pour séparer des pièces assemblées depuis longtemps sans les détériorer.
Ces outils de haute précision permettent de préserver l'intégrité des équipements et facilitent leur remontage ultérieur. Leur utilisation requiert une formation spécifique et une grande expertise technique.
Gestion des risques et conformité réglementaire
La gestion des risques et le respect de la réglementation sont des aspects cruciaux du déménagement industriel. Ces éléments doivent être intégrés à chaque étape du processus pour garantir la sécurité des personnes et la conformité légale de l'opération.
Une analyse de risques approfondie doit être réalisée en amont du projet. Elle couvre les aspects liés à la sécurité du travail, à la protection de l'environnement et à la préservation des équipements. Cette analyse permet d'identifier les points critiques et de mettre en place des mesures préventives adaptées.
La conformité réglementaire implique le respect de nombreuses normes, notamment en matière de transport de matières dangereuses, de gestion des déchets industriels et de sécurité des installations. Des experts en réglementation industrielle doivent être impliqués pour s'assurer que toutes les obligations légales sont respectées tout au long du processus de déménagement.
La prévention des risques et la conformité réglementaire ne sont pas des options, mais des impératifs absolus dans tout projet de déménagement industriel.
La formation du personnel aux procédures de sécurité spécifiques au déménagement est également essentielle. Des sessions de sensibilisation et des exercices pratiques doivent être organisés pour préparer les équipes aux situations à risque potentielles.
Continuité opérationnelle pendant la transition
Assurer la continuité opérationnelle pendant la phase de transition est un défi majeur du déménagement industriel. Cette période critique nécessite une gestion fine des ressources et une adaptation rapide aux nouvelles conditions de production.
La mise en place d'un plan de continuité d'activité (PCA) est indispensable pour anticiper et gérer les perturbations potentielles. Ce plan identifie les processus critiques qui doivent être maintenus à tout prix et prévoit des solutions de repli en cas de problème.
La gestion des stocks joue un rôle clé dans la continuité opérationnelle. Il est souvent nécessaire de constituer des stocks tampons plus importants pour absorber les fluctuations de production pendant la période de transition. Cette approche doit être soigneusement équilibrée pour éviter les surcoûts de stockage tout en garantissant la satisfaction des clients.
La communication avec les clients est également cruciale pendant cette phase. Il est important de les informer des changements à venir et de les rassurer sur la capacité de l'entreprise à honorer ses engagements. Dans certains cas, des arrangements spéciaux peuvent être négociés pour adapter temporairement les délais de livraison.
L'adaptation des systèmes d'information et de gestion de la production au nouveau site est un autre aspect critique de la continuité opérationnelle. Les logiciels de GPAO
(Gestion de Production Assistée par Ordinateur) et de MES
(Manufacturing Execution System) doivent être reconfigurés pour refléter la nouvelle organisation de la production.
La flexibilité et la réactivité sont les maîtres-mots pour assurer une transition en douceur et maintenir la productivité pendant le déménagement industriel.
Enfin, la formation du personnel à leurs nouvelles conditions de travail est essentielle pour une reprise rapide de la production. Des sessions de formation sur site doivent être organisées dès que possible pour familiariser les opérateurs avec leur nouvel environnement et les éventuelles modifications des procédures de travail.
En conclusion, le déménagement industriel est une opération complexe qui nécessite une expertise multidisciplinaire et une planification rigoureuse. La maîtrise de la logistique spécialisée, la coordination précise des opérations, l'utilisation de technologies avancées, la gestion des risques et l'assurance de la continuité opérationnelle sont les piliers d'un transfert industriel réussi. En accordant l'attention nécessaire à chacun de ces aspects, les entreprises peuvent transformer ce défi en une opportunité d'optimisation et de modernisation de leurs processus de production.